Introducción
En los siguientes 10 años, las producciones pecuarias e industria de alimento balanceado tendrán que producir suficiente carne, leche y huevo para alimentar a 8.5 billones de personas. Debido a que nuestro planeta tiene recursos limitados, el desafío de la industria avícola será producir carne y huevo de una forma más eficiente. Además, los costos de alimentación representan del 60% al 70% del total de costos de la industria avícola, lo cual desafía a los productores a encontrar estrategias nutricionales y de procesamiento efectivas, eficientes y que les permita obtener retornos económicos. Cada uno de los pasos en la elaboración de alimento balanceado, es decir recepción de ingredientes, molienda, pesado, dosificación, mezclado, peletizado, enfriamiento y embolsado, puede tener un efecto positivo o negativo en el desempeño de las aves. Este artículo discutirá como cada área dentro de la fabricación del alimento balanceado puede influenciar el desempeño productivo de las aves.
Recepción de ingredientes
La recepción de ingredientes es la primera línea de defensa dentro de un programa de control de calidad. La calidad de los ingredientes no puede ser mejorada después del recibo. Ingredientes de baja calidad son más difíciles de manejar en la fábrica ya que son más propensos al crecimiento de moho y producción de micotoxinas; por consiguiente, el personal de recibo debe determinar primero si el ingrediente es adecuado para descargarse y estar presente durante todo el proceso de descarga. El muestreo y la evaluación de las características físicas de los ingredientes como color, textura, olor, humedad y presencia de materiales extraños antes de la descarga, es esencial para la producción de alimentos balanceados de alta calidad. Las fábricas de alimento balanceado también deben monitorear el nivel de micotoxinas de acuerdo con sus programas de calidad y rechazar ingredientes que no cumplan con las especificaciones de calidad. Un muestreo adecuado puede ayudar al gerente de la fábrica a rechazar ingredientes que no satisfagan los requerimientos físicos o nutricionales. Recientemente, la industria ha incrementado los esfuerzos para implementar “Espectroscopia del Infrarrojo Cercano” (NIR por sus siglas en inglés), para cuantificar humedad, proteína, nivel de amino ácidos, fibra y grasa de los ingredientes. Esta herramienta puede ayudar a los nutricionistas y formuladores a actualizar sus matrices nutricionales con más frecuencia y producir alimentos que satisfagan los requerimientos nutricionales de las aves de acuerdo con su edad, tipo y fase productiva; así mismo, los resultados de los análisis, pueden ayudar a separar ingredientes con base en su valor nutricional (Stark y Jones, 2015).
Molienda
La mayoría de los ingredientes en dietas para aves requieren de algún tipo de molienda. Cereales como el maíz y el trigo son molidos en la fábrica de alimentos balanceados, mientras que otros ingredientes como harina de soya, fuentes de calcio y fósforo, granos secos de destilería con solubles (DDGS por sus siglas en inglés), son recibidos ya molidos. La molienda es la primera etapa del proceso de fabricación de alimentos balanceados (Behnke, 1983). El proceso de molienda es importante para incrementar el área superficial de los ingredientes, lo cual incrementa su interacción con enzimas digestivas, promueve un mejor mezclado y reduce la segregación de nutrientes después del mezclado, particularmente en dietas alimentadas en harina. Sin embargo, a medida que el tamaño de partícula disminuye, el costo de la molienda incrementa y la tasa de molienda (ton/hr) disminuye (Wondra et al., 1995). Los molinos de martillos son los principales equipos de molienda en dietas peletizadas. Los molinos de rodillos, son más usados en dietas que van a ser alimentadas en harina, ya que producen partículas más uniformes con menos porcentaje de finos. La selección del equipo de molienda debe estar basada en los tipos de granos a molerse, tamaño de partícula deseado y presentación del alimento a producirse.
Una de las principales desventajas de los molinos de martillos es que crean una cantidad considerable de partículas finas (<400 µm). El uso de variadores de frecuencia (VFD por sus siglas en inglés) en el motor de accionamiento principal de los molinos de martillos, puede ayudar a controlar el tamaño de partícula, por medio del ajuste de la velocidad de la punta de los martillos.
Figura 1: Ilustración de variadores de velocidad en los molinos de martillo y su efecto en la velocidad de punta de los martillos.
Molienda muy fina puede ocasionar gran cantidad polvo, pérdidas de humedad y causar problemas de flujo durante el proceso de manufactura. Ingredientes con tamaño de partícula muy fina en dietas para pollos de engorde pueden ocasionar una tasa de pasaje gastrointestinal alta, lo que puede conllevar a una reducción en la digestibilidad de nutrientes y ocasionar problemas de salud intestinal. A diferencia de los mamíferos, las aves tienen un tracto intestinal más corto, lo cual resulta beneficioso en condiciones normales ya que el costo energético de volar incrementa con el peso del tracto gastrointestinal (Caviedes-Vidal et al., 2007); por ende, las aves han evolucionado para tener un órgano de molienda o “molleja” para compensar su corto tracto gastrointestinal.
De acuerdo con Ferket (2000), una molleja bien desarrollada mejora la motilidad del intestino, incrementa el tiempo de retención del alimento en el tracto gastrointestinal, promueve una mejor digestión y absorción de nutrientes y reduce el riesgo de coccidiosis y otras enfermedades entéricas. Adicionalmente, la incorporación de partículas gruesas en dietas para aves incrementa la digestibilidad de nutrientes y modifica la micro-flora en el intestino a través de un incremento en el número de bacterias benéficas y/o una reducción de bacterias patógenas (Gabriel et al., 2003). Partículas gruesas incrementan el peristaltismo reverso entre la molleja y el proventrículo, incrementando la secreción de ácido clorhídrico por el proventrículo y reduciendo el pH de la molleja, lo cual puede inactivar bacterias patógenas como Salmonella spp.y Clostridium perfringens antes de que ingresen al intestino delgado (Engberg et al., 2002; Bjerrum et al., 2005). Xu et al. (2015) evaluaron el efecto de reemplazar 50% de maíz grueso con un tamaño de partícula promedio de 1,359 µm por maíz molido con un tamaño de partícula de aproximadamente 450 µm, durante los periodos de crecimiento y finalización. La eficiencia alimenticia, digestibilidad de nutrientes, peso de molleja, y relación molleja/proventrículo mejoró significativamente, cuando 50% de maíz grueso se usó para reemplazar 50% del maíz fino en las dietas (Tabla 1). Reemplazar 50% del maíz fino por maíz grueso también mejoró la compartimentación entre la molleja y el proventrículo, lo cual sugiere un mejor balance entre la actividad enzimática y secreción de ácidos en el proventrículo y molienda en la molleja. También el reemplazo de 50% de maíz grueso en lugar de 50% maíz fino, redujo el contenido de nitrógeno en la cama y mejoró la digestibilidad de la energía. La reducción de nitrógeno es importante para reducir la incidencia de podo dermatitis, particularmente en condiciones de alta humedad de cama.
Tabla 1. Efecto de la inclusión de maíz grueso en la dieta sobre el desempeño productivo, desarrollo de órganos, condición de cama y digestibilidad de nutrientes a los 49 días de edad.
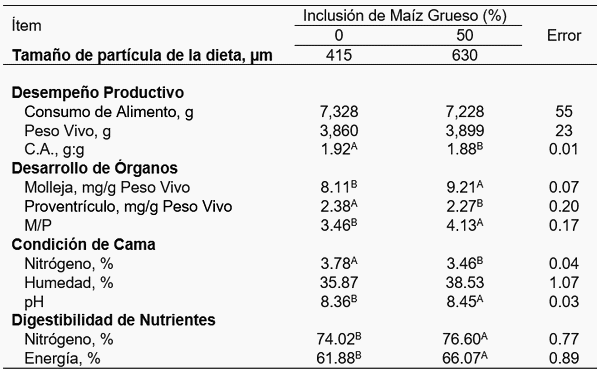
El tamaño de partícula de harina de soya también influye en el rendimiento de pollo de engorde. Kilburn y Edwards (2004) reportaron una mejora en digestibilidad de minerales cuando el tamaño de partícula de harina de soya se incrementó de 891 µm a 1,239 µm. Pacheco et al. (2014) evaluaron el efecto de tamaño de partícula (530 y 1,300 µm) y niveles de inhibidores de tripsina (6, 9, 12, 15, 18 y 21 unidades de inhibidores de tripsina/mg) de soya integral en el crecimiento de pollos de engorde de 1 a 14 días de edad y reportaron que el incremento de tamaño de partícula de soya integral mejoró el crecimiento de los pollos de engorde, especialmente cuando los niveles de inhibidores de tripsina fueron arriba de 9 UIT/mg (Figura 1). Según los autores, la molienda gruesa de soya integral posiblemente incrementó el peristaltismo gástrico reverso (molleja y proventrículo), lo que causó la desnaturalización ácida de los inhibidores de tripsina, incrementó el movimiento de bilis a la molleja (Figura 2), liberó los inhibidores de tripsina de una manera más lenta o constante y, consecuentemente, esto le dió a las aves la oportunidad de adaptarse a la exposición a inhibidores de tripsina.
Figura 2. Efecto del nivel de inhibidores de tripsina y tamaño de partícula (1,300 µm; grueso y 530 µm; fino) de la harina de soya en la ganancia de peso de pollos de engorde de 1 a 14 días de edad.
Figura 2. Descripción gráfica del movimiento de bilis hacia la molleja producto de la peristalsis gástrica inversa.
Los resultados de varios estudios científicos indican que el tamaño de partícula de los ingredientes en alimentos para aves influencia su rendimiento productivo y los costos de molienda. Por lo tanto, se debe hacer un análisis del tamaño de partícula por lo menos semanalmente, después de realizar cualquier mantenimiento preventivo y/o correctivo en el equipo de molienda como cambiar zarandas, cambiar martillos/rodillos y o cuando cambian las características del maíz (e.g. nueva cosecha de maíz).
Análisis de tamaño de partícula
El método utilizado para medir el tamaño de partícula de los granos es el “Método de determinación y expresión de la finura de los materiales del alimento por tamizado” (ASABE S319.4). Este método permite diferentes variaciones como ser; uso de agitadores de tamiz y uso de agentes de dispersión. Según Kalivoda y Stark (2016), variaciones en la metodología del análisis de tamaño de partícula pueden impactar significativamente en el resultado final (Tabla 2). Por lo tanto, es importante que los investigadores, nutricionistas y gerentes de fábricas de alimento balanceado, comprendan el método utilizado por el laboratorio que realiza el análisis del tamaño de partícula. De otra manera, la interpretación de los datos podría dificultarse debido a la significativa variación que existe entre métodos.
Tabla 2. Efecto del método de análisis de tamaño de partícula sobre el diámetro medio geométrico (dgw) y la desviación estándar geométrica (Sgw)
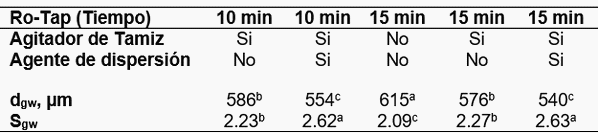
Pesaje, Dosificación y Mezclado
El objetivo principal de los procesos de pesado, dosificado y mezclado es producir alimentos en los que los nutrientes, aditivos y medicamentos (en caso se requieran) se distribuyan uniformemente en el menor tiempo posible. El proceso de mezcla es bastante simple y consiste en transferir los ingredientes pesados a una mezcladora, mezclar durante un tiempo sin líquidos (conocido como fase de mezclado seco), agregar líquidos y luego mezclar para la fase de “mezclado húmedo”. Los tiempos de mezclado seco y húmedo varían dependiendo del tipo de mezcladora, pero como consideración general, el mezclado en seco representa aproximadamente 20% del tiempo total de mezclado. Por ejemplo, para una mezcladora de doble cinta, el tiempo de mezclado en seco es de aproximadamente 30 segundos, mientras que el mezclado en húmedo es de aproximadamente 120 segundos. Producir un alimento uniforme es extremadamente importante, principalmente durante las fases de pre-inicio e inicio en pollos de engorde o pollitas debido al bajo consumo de alimento en estas fases. Por ejemplo, los pollitos recién nacidos consumen alrededor de 12 gramos de alimento durante el primer día; por lo tanto, tienen que recibir todos los nutrientes necesarios (vitaminas, minerales, proteínas, carbohidratos y grasas) en esa cantidad de alimento. Además, es importante tener en cuenta que los alimentos para aves, están destinados a ser la fuente única de nutrientes y cualquier deficiencia o toxicidad causada por una mezcla deficiente afectará negativamente su rendimiento y salud. Aunque el mezclado es simple, hay muchos problemas potenciales que pueden ocurrir, tales como: sobrellenar el mezclador debido a cambios en la densidad de los ingredientes (por ejemplo: incremento en el uso de salvado de trigo), acumulación en las cintas o paletas que restrinjan el flujo de material y reduzcan la capacidad e la mezcladora, rociar líquidos en las cintas o paletas, tiempo de mezclado seco y/o húmedo demasiado corto, orden incorrecto de adición de ingredientes al mezclador, compuertas con fugas, cintas o paletas rotas y rotación inversa del mezclador.
Antes de empezar a contar el tiempo de mezclado, los ingredientes con mayor nivel de inclusión (e.g. maíz, soya) deben adicionarse primero a la mezcladora, seguidos de los de menor volumen (e.g. fosfatos, harinas de origen animal, etc.) y por último los micro ingredientes (vitaminas, minerales, aminoácidos, aditivos), con un pequeño espacio después de cada adición. Si hay ingredientes que son pesados manualmente, estos deben adicionarse, después que los micro ingredientes hayan ingresado al mezclador. Los posibles problemas de mezcla se pueden identificar y solucionar con mantenimiento preventivo y correctivo, inspecciones visuales y pruebas de uniformidad de mezclado.
Las fábricas de alimento balanceado que usan una cantidad significativa de ingredientes líquidos deben evaluar rutinariamente la uniformidad de la mezcla de los líquidos, además de las pruebas estándar para ingredientes secos. Los ingredientes líquidos se deben aplicar por medio de boquillas que garanticen un buen patrón de aspersión tipo abanico; un tubo con perforaciones no podría cumplir con estos requerimientos.
Pruebas de Uniformidad de Mezclado
Se debe evaluar la uniformidad de mezclado después la instalación de los equipos y al menos una vez al año para determinar los tiempos óptimos de mezclado seco y húmedo. La uniformidad de mezclado se estima por el coeficiente de variación (CV) de un nutriente o ingrediente específico, generalmente cloro proveniente de la sal, minerales traza como ser manganeso y/o aminoácidos sintéticos como lisina, metionina y treonina. La uniformidad del mezclador se usa para medir el grado de dispersión de los ingredientes en un lote de alimento. Se recomienda que el CV no sea mayor al 10%.
Antes de hacer el análisis de mezclado, se deben tomar 10 muestras representativas directamente de la mezcladora, de la tolva de compensación o durante la descarga de la mezcladora. Luego, todas las muestras deben analizarse para determinar la uniformidad de la mezcla. El coeficiente de variación de la mezcla se calcula dividiendo la desviación estándar por la media aritmética de las muestras y luego multiplicándola por 100. Herrman y Benhke (1994) proporcionaron pautas para interpretar y corregir problemas relacionados con la uniformidad de mezclado (Tabla 3). Es importante reevaluar la uniformidad de mezclado después de tomar una acción correctiva para garantizar que la acción correctiva corrigió el problema.
Tabla 3. Interpretación de la uniformidad de mezclado y acciones correctivas
Peletizado
Durante el peletizado, ingredientes o alimentos mezclados son aglomerados y moldeados usando vapor (que proporciona calor y humedad) y presión colocada entre un troquel/dado y dos o tres rodillos, según el diseño de la peletizadora. Debido a que más del 80% de los alimentos balanceados para no rumiantes en los EE. UU. se presentan en forma de pellet, es importante garantizar una buena calidad de estos hasta su consumo (Behnke, 2001; Parsons et al., 2006). Los beneficios del peletizado incluyen una mejora en ganancia diaria de peso, mejor conversión alimenticia, mejor uniformidad de las aves, mejor digestibilidad del alimento, reducción de la segregación de nutrientes, reducción de alimentación selectiva y reducción de carga microbiana, lo cual va a depender de la combinación de temperatura de acondicionamiento y tiempo de retención en el acondicionador (Benhke, 1994).
Una de las principales razones para utilizar dietas peletizadas es aumentar el consumo de alimento. Un mayor consumo permite que los pollos de engorde cumplan con sus requisitos de mantenimiento (respiración, circulación sanguínea, termorregulación, función inmune, etc.) con un pequeño porcentaje de la ingesta diaria, utilizando el resto de nutrientes para crecimiento y desarrollo de pechuga. La calidad del pellet es crucial para garantizar un rendimiento óptimo de las aves. A medida que disminuye la calidad de los pellets (más finos o menos pellets enteros), hay una disminución en el peso corporal, eficiencia alimenticia y uniformidad. La mala calidad de los pellets obliga a las aves a pasar más tiempo en el comedero y menos tiempo descansando. Las más agresivas en la parvada pasan más tiempo en el comedero, dejando menos tiempo de alimentación para las menos agresivas, lo que se traduce en una pobre eficiencia productiva y una menor uniformidad.
La calidad del pellet está influenciada por la formulación, tamaño de partícula de los ingredientes, temperatura y tiempo de retención durante el acondicionamiento, especificaciones del dado y enfriamiento y secado (Behnke, 1994). Sin embargo, los gerentes de las fábricas de alimento balanceado tienen responsabilidades limitadas de toma de decisiones relacionadas con las formulaciones de alimentos y el tamaño de partícula de los ingredientes; muchas fábricas de alimentos no tienen la capacidad de agregar grasa post peletización. Además, la formulación del alimento generalmente se enfoca en formular una dieta que cumpla o exceda los requerimientos nutricionales de las aves a una edad, peso y/o fase de producción específica, con una consideración mínima o nula relacionada a la calidad de los pellets. La adición de enzimas exógenas como fitasa, puede mejorar la digestibilidad del fósforo, pero esto puede tener un efecto negativo en la peletización debido a una disminución en el uso de fuentes de fosfato inorgánico, que ayudan a limpiar el dado y a mejorar el rendimiento de la peletizadora.
Para garantizar una buena calidad de pellets, los gerentes de las fábricas de alimento balanceado deben centrarse en administrar eficientemente el sistema de peletización desde el acondicionamiento hasta el enfriamiento. A medida que el alimento en harina ingresa al acondicionador y entra en contacto con el vapor, el calor del vapor se transfiere a la partícula, lo que hace que su temperatura y humedad aumenten. Una vez que se produce la condensación de vapor en la superficie, tanto el calor como la humedad comienzan a migrar hacia el centro de las partículas. El tiempo de retención en el acondicionador se vuelve más crucial a medida que se aumenta el tamaño de partícula de los ingredientes, ya que la humedad y el calor necesitan más tiempo para ser absorbidos y llegar al centro. Además, el vapor y la humedad son necesarios para la gelatinización del almidón, desnaturalización de proteínas, adhesión de partículas y reducción de patógenos. Después de que el alimento se acondiciona, ingresa a la cámara de peletización. El grosor efectivo del dado es importante ya influencia el nivel de compresión de la harina. Dados de mayor grosor tienen un impacto positivo en la calidad del pellet al aumentar la fricción entre las partículas del alimento y la pared, lo que aumenta la gelatinización del almidón en la superficie de los pellets. Los dados deben protegerse en todo momento, inspeccionando los magnetos que se usan para remover metales y manteniendo cerradas las puertas de los silos de harina en todo momento para evitar la introducción accidental de metal.
Los pellets que salen de la peletizadora están calientes y húmedos, además son frágiles y fáciles de romper. El enfriamiento deber incluir el manejo cuidadoso de los pellets y la eliminación adecuada de humedad para un almacenamiento seguro. La altura de la cama de los pellets y el flujo de aire durante el enfriamiento deben ser controlados. El enfriamiento demasiado rápido puede conllevar a la eliminación rápida de más humedad y calor en la superficie de los pellets, dejando el centro húmedo. Si esto ocurre, la humedad del centro de los pellets empieza a migrar a la superficie, lo que puede resultar en pellets con mayor contenido de humedad y más frágiles. Como regla general, la temperatura de los pellets no debe ser superior a 10°F (5.5°C) por encima de la temperatura ambiente y la humedad debería ser de ± 0.5% del alimento en harina original. Durante el enfriamiento, es crucial inspeccionar visualmente la profundidad y la uniformidad de la cama de los pellets y asegurarse que no hay variaciones. La uniformidad de la profundidad de la cama de pellets es muy importante ya que las variaciones pueden crear disparidades en la temperatura, contenido de humedad y calidad de los pellets del producto enfriado.
El último indicador del rendimiento del sistema de peletización es el Índice de durabilidad de pellet. El propósito del análisis de durabilidad de los pellets es simular el manejo de estos desde la fábrica de alimentos balanceados hasta la granja y predecir la calidad de los pellets (cantidad de finos versus pellets enteros) frente a las aves en el nivel del comedero. Las mediciones de durabilidad de los pellets deben realizarse de manera regular y es recomendable tomar muestras y analizar la calidad una vez que el sistema esté funcionando de manera constante (15 a 30 minutos después del comienzo de la peletización). De esta manera, se pueden hacer ajustes antes de que sea demasiado tarde. Además, se deben tomar muestras de al menos 800 gramos de alimento para asegurar que haya 500 g de pellets tamizados limpios disponibles para las pruebas. Pacheco et al. (2009) demostraron una relación directa entre el peso inicial de la muestra y los resultados de calidad de pellet. Su estudio confirmó que se deben usar 500 g de pellets enteros al analizar calidad de pellets para poder comparar con otras fábricas de alimento balanceado. También es una buena idea controlar ocasionalmente la cantidad de finos presentes que salen de la peletizadora, enfriadora, varios equipos de manipulación y los silos de alimento terminado para evaluar si se está produciendo una degradación significativa de los pellets en el proceso.
Figura 2. Efecto del peso de la muestra en el Índice de Durabilidad de Pellet (IDP)
La peletización es un proceso costoso y la calidad del alimento peletizado tendrá un impacto significativo en el rendimiento de las aves.
Crumbler (migajadora) y calidad de crumble (migajas)
Debido a las limitaciones en el tamaño del pico, pollitos recién nacidos no pueden consumir fácilmente pellets enteros. Por lo tanto, se deben ofrecer crumblers o micropellets durante los períodos de pre-inicio e inicio. El crumbler se usa en fábricas de alimento balanceado para fraccionar los pellets en pequeñas partes sin producir cantidades excesivas de partículas finas que sean menores de 1 mm. Según Michard y Rouxel (2015), los pollitos pequeños prefieren partículas entre 1.5 y 2.0 mm. En un estudio más reciente, Rubio et al. (2019) evaluaron el efecto de la forma de alimentación (harina, crumbles y micropellets de 3.0 mm) durante el período inicial (1 a 14 días) en rendimiento del pollo de engorde y rendimiento del procesamiento a los 35 días. Los autores reportaron que los pollos de engorde alimentados con dietas de harina durante el período de inicio tenían un menor peso corporal y una menor ingesta de alimento a los 14 y 35 días y aproximadamente 30 gramos menos de peso de la pechuga a los 35 días, en comparación con los pollos alimentados con crumbles o micropellets de 3.0 mm. Para producir crumbles uniformes, los rodillos deben alinearse con el mismo espacio a lo ancho del crumbler. Además, los pellets deben entrar de manera uniforme a lo ancho de los rodillos para promover un desgaste uniforme. Una distribución de pellet inconsistente o desigual podría resultar en un desgaste desigual de los rodillos y afectar negativamente la calidad del crumble. Según el manual de manejo de pollos de engorde de Aviagen, el tamaño de los crumbles debe ser: 15% más de 3 mm, 40% entre 2 y 3 mm, 35% entre 1 y 2 mm y 10% menos de 1 mm.
Pocos estudios han evaluado el efecto del tamaño y la calidad del crumble en el rendimiento del pollito. Sin embargo, los crumbles con un alto nivel de finos (partículas de menos de 1 mm de tamaño) podrían aumentar el desperdicio de alimento, reducir la eficiencia del alimento, aumentar el polvo en el interior del galpón y aumentar el consumo de agua, lo que puede conducir a malas condiciones de cama y aumentar el riesgo de podo dermatitis en las almohadillas de las patas. Por otro lado, los crumbles gruesos (partículas de más de 3 mm de tamaño) podrían estimular el consumo selectivo y contribuir a la segregación del alimento.
La producción eficiente de carne y huevo requiere un enfoque integrado, por lo tanto, cada área de producción debe gestionarse de manera eficiente. La producción de alimento de alta calidad para aves comienza con ingredientes de alta calidad, que deben ser molidos a un tamaño de partícula específico, pesados con precisión, mezclados uniformemente y peletizados con una cantidad mínima de finos. La industria avícola tiene el desafío de mantenerse competitiva, producir alimentos seguros y alimentar a mil millones de personas más en los próximos 15 años.