Cómo optimizar el rendimiento y minimizar los costos de mantenimiento en los procesos de molienda.
Independientemente de la aplicación, el rendimiento dependerá en gran medida del adecuado dimensionamiento y correcto funcionamiento del molino o molino. Este artículo describe los parámetros críticos y los elementos de mantenimiento básico para estas máquinas reductoras de tamaño comunes.
Fundamentos de la molienda en molinos de martillos.
Un molino de martillos típico, como se muestra en la Figura 1, consta de un rotor encerrado en una cámara de molienda cilíndrica rodeada de cribas. El rotor está ensamblado con una serie de barras metálicas planas, llamadas martillos, que giran a alta velocidad a través de la cámara de molienda a medida que el material ingresa al molino. Los martillos impactan el material rompiendo las partículas y las partículas reducidas pasan a través de las cribas para salir del molino.
Figura 1: Operación típica de un molino de martillos. Imagen cortesía de CPM Américas.
La versatilidad y facilidad de operación hacen del molino de martillos una excelente opción para muchas aplicaciones de reducción del tamaño de partículas. Mantener los costos operativos y de mantenimiento al mínimo requiere una comprensión de las variables clave que intervienen en su operación.
Velocidad de la punta
La mayor parte de la molienda que ocurre en un molino de martillos ocurre cuando los martillos impactan el material por primera vez (Figura 1). La velocidad a la que giran los martillos se llama velocidad punta. Las velocidades de punta más rápidas (> 20 000 pies por minuto) son más eficientes para producir moliendas más finas. Esto se debe a que se pueden utilizar tamices con diámetros de orificio más grandes, lo que permite que salga más material de la cámara de molienda. Sin embargo, velocidades de punta más rápidas con cribas más grandes producirán partículas más finas y material de gran tamaño, lo que resultará en una mayor variación en el tamaño de las partículas. Por otro lado, velocidades de punta más lentas con cribas de diámetro de orificio más pequeño producirán una molienda más uniforme.
Área de la pantalla
Los molinos de martillos se dimensionan utilizando una relación entre el área de la criba y la potencia conectada. Para la mayoría de las aplicaciones, la relación preferida es 14 in²: 1 hp. Algunas aplicaciones, como productos con una densidad aparente más baja, pueden requerir un área de criba mayor por caballo de fuerza. Como resultado, los molinos de martillos con una proporción inferior a 12 in²: 1 hp pueden experimentar un desgaste prematuro del martillo. Por esta razón, instalar un motor más grande en un molino existente puede no ser la mejor opción para aumentar la capacidad.
Diámetro del orificio de la pantalla
Como regla general, cuanto mayor sea el diámetro del orificio en la criba de un molino de martillos, más gruesa será la molienda y viceversa. Sin embargo, la pantalla no siempre es la mejor variable para cambiar y obtener un tamaño de molienda diferente. El patrón del martillo y la velocidad de la punta juegan un papel más importante en el tamaño de las partículas que las cribas. Como se mencionó anteriormente, las cribas más grandes producen una molienda más gruesa con mayor rendimiento, pero también dan como resultado una mayor variación en el tamaño de las partículas. El tamaño del tamiz afecta el extremo más grande de la distribución del tamaño de las partículas más que el extremo más fino, pero en cierto punto, dependiendo de la aplicación, el uso de un tamiz más grande no dará como resultado una molienda más gruesa debido al gran papel que desempeña. de los martillos y la velocidad de la punta en el proceso.
Patron de martillo
El patrón de martillo simplemente se refiere a la cantidad de martillos instalados en el molino de martillos. Así como la relación entre el área de la criba y los caballos de fuerza se utiliza para determinar el tamaño del motor, se utiliza una relación de caballos de fuerza por martillo para determinar cuántos martillos instalar en el molino. Las proporciones más altas darán como resultado un molido grueso, mientras que las proporciones más bajas producirán un molido más fino. Una proporción demasiado alta (> 2,5 hp/martillo) puede reducir la vida útil del martillo. Si el cuerpo o el orificio del pasador del martillo están desgastados antes del recargue o si hay ranuras excesivas en los pasadores del martillo, una solución común es aumentar el número de martillos. Los patrones de martillo más comunes varían de 1,4:1 a 1,9:1 hp/martillo.
Posición de los martillos
La mayoría de los rotores de molinos de martillos tienen dos conjuntos diferentes de orificios para pasadores. La posición gruesa está más cerca del centro del rotor, mientras que la posición fina está más cerca del exterior del rotor. Estas posiciones cambian el espacio libre entre la punta del martillo y el interior de las rejillas. La principal diferencia entre estas posiciones es el ángulo de salida del material, donde la posición gruesa proporciona una ruta más directa para que el material molido salga de la cámara de molienda, como se muestra en la Figura 2. La posición gruesa es más eficiente en términos de energía que la fina. configuración.
Figura 2: La posición del martillo grueso proporciona una ruta más directa para que el material molido salga de la cámara de molienda y es más eficiente energéticamente que la posición fina. Imagen cortesía de CPM Américas.
Aspiración
Tener un volumen adecuado de aire (llamado aspiración) que fluya a través del molino es crucial para un proceso eficiente. La aspiración elimina las partículas molidas de la cámara de molienda. Una succión insuficiente mantiene el material en la cámara de molienda por más tiempo, lo que provoca un aumento de partículas finas, desgaste prematuro del martillo y reducción de la eficiencia. Para calcular la succión requerida (medida en pies cúbicos por minuto [cfm]), el área de la criba del molino se multiplica por 1,25 a 1,5, según la aplicación. Por ejemplo, un molino de martillos con 3600 in² de área de criba requerirá de 4500 a 5400 cfm de succión.
Condiciones ambientales
La temperatura ambiente y la humedad pueden afectar el rendimiento del molino de martillos. A medida que aumenta la temperatura y/o la humedad del material, también aumenta la energía necesaria para triturar el material. Por el contrario, a medida que disminuye la temperatura y/o la humedad del material, el material se vuelve más fácil de moler. Esta es la razón por la que un material puede requerir más energía para molerse durante los meses calurosos y húmedos del verano que durante los fríos y secos meses del invierno.
Elementos básicos de mantenimiento del molino de martillos
Los siguientes pasos de mantenimiento ayudarán a optimizar el proceso de su molino de martillos:
• Reemplace periódicamente los artículos desgastados, como cribas y martillos. Los costos de energía son mayores que los costos de piezas. A medida que las piezas se desgastan, la eficiencia de la máquina disminuye. Esperar demasiado para reemplazar los elementos desgastados puede ahorrar en costos de piezas, pero aumentará los costos operativos durante la vida útil de la máquina. Reemplazar martillos y cribas cuando el costo de la pérdida de producción debido a una menor eficiencia sea mayor que el costo de las piezas de repuesto.
• Cambie con frecuencia la dirección de rotación del rotor para asegurar un desgaste uniforme en ambos lados de los martillos y los orificios de la criba. Nunca gire el rotor del molino de martillos en la misma dirección durante más de 2 semanas.
• Mantenga materiales extraños fuera del molino de martillos. Cualquier material que no esté destinado a ser fresado provocará un desgaste prematuro de los componentes del molino. Limpie los imanes del separador con frecuencia.
• Inspeccione visualmente la máquina siempre que esté abierta. Busque desgaste desigual en las piezas, que puede deberse a una alimentación desigual a lo ancho del molino. Otro problema común es el desgaste de las piezas del alimentador que no dosifican correctamente el material al molino de martillos. Identificar un problema antes de que se convierta en un problema mayor puede ahorrarle dinero en términos de repuestos, costos de mano de obra y tiempo de inactividad.
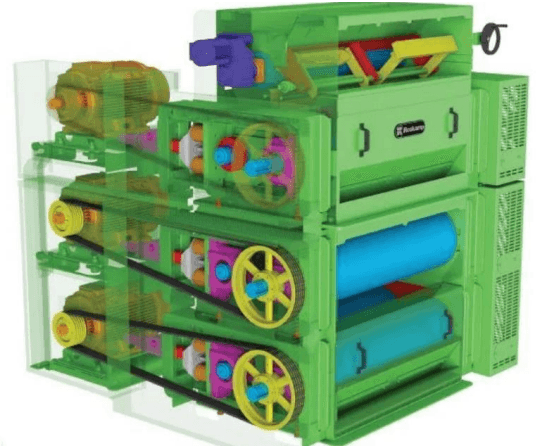
Fundamentos de la molienda en molinos de rodillos.
En un molino de rodillos, el material se alimenta desde la parte superior a una ranura estrecha (llamada línea de contacto) entre rodillos cilíndricos
giratorios, que muelen el material hasta obtener el tamaño de partícula deseado. Los molinos de rodillos se pueden configurar con uno, dos o tres pares de rodillos, según la aplicación.
En comparación con los molinos de martillos, los molinos de rodillos pueden producir una molienda más uniforme a un costo operativo mucho menor, pero no pueden lograr una molienda tan fina. La Figura 3 muestra un análisis granulométrico para la molienda realizada mediante un molino de martillos y un molino de rodillos. Cada molienda produjo una distribución con un diámetro de partícula promedio de aproximadamente 710 micrones, pero la distribución del Molino de Rodillos está más concentrada que la distribución del Molino de Martillos.
Figura 3: La distribución del tamaño de partículas de una trituradora de rodillos está más concentrada que la distribución del tamaño de partículas de un molino de martillos. Imagen cortesía de CPM Américas.
Las principales áreas a considerar en los molinos de rodillos son el tamaño de los rodillos, las corrugaciones, la diferencia de velocidad entre los rodillos, el paralelismo de los rodillos y la planitud de los rodillos.
Tamaño de los rollos
El tamaño de los rodillos en un molino de rodillos es el factor más importante a la hora de determinar la capacidad de la máquina, y los rodillos más grandes proporcionan una mayor capacidad. Sin embargo, la capacidad de molienda no es el único factor y los rodillos pueden ser muy largos. Los rodillos de mayor diámetro son más ventajosos que los de menor diámetro por tres razones principales: un ángulo de sujeción más óptimo, mayor superficie del rodillo y menor deflexión del rodillo.
Ángulo de sujeción. Los rodillos de mayor diámetro reducen el ángulo de pellizco entre los rodillos y permiten que los rodillos agarren el material de manera más eficiente y lo arrastren a través de los rodillos de abajo.
Área superficial de los rodillos. Una mayor superficie reduce la frecuencia con la que es necesario retirar y reesculturar los rollos, lo que reduce los costos de mano de obra y el tiempo de inactividad. Por ejemplo, un rollo de 16 x 36 pulgadas tiene un 33 % más de superficie que un rollo de 12 x 36 pulgadas, por lo que el rollo de 16 x 36 pulgadas puede procesar un 33 % más de material que el rollo de 12 x 36 pulgadas antes de necesitar ser reesculturado.
Deflexión del rodillo. La deflexión del rollo se refiere a cuánto puede flexionarse el centro del rollo. Los rodillos se apoyan únicamente en cada extremo donde los cojinetes están unidos al bastidor de la máquina. La deflexión es un factor tanto de la longitud como del diámetro del rollo. Los rollos de 16x52 pulgadas pueden flexionarse 0,0006 pulgadas por rollo, mientras que los rollos de 12x52 pulgadas pueden flexionarse hasta 0,002 pulgadas por rollo y los rollos de 12x72 pulgadas pueden flexionarse hasta 0,005 pulgadas por rollo (Figura 4). Por esta razón, no se recomienda utilizar un rodillo de más de 52 pulgadas para aplicaciones que requieren un pulido uniforme. Los rollos de más de 52 pulgadas solo deben usarse cuando el material se procesará más después del paso de molienda. Además, utilice un rodillo de mayor diámetro posible para mantener el material molido lo más uniforme posible.
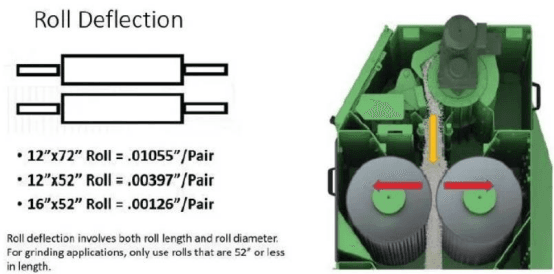
Figura 4: La deflexión se refiere a cuánto puede flexionarse el rodillo en el centro cuando el material pasa por el molino. Imagen cortesía de CPM Américas.
Corrugaciones
Las corrugaciones de los rodillos deben seleccionarse de acuerdo con los materiales a procesar y los requisitos del producto final. Las corrugaciones más gruesas ofrecen una vida útil más larga y mayores capacidades, pero producirán productos finales cada vez más gruesos. Las corrugaciones más delgadas darán como resultado productos finales más delgados, pero reducirán la capacidad y se desgastarán más rápidamente. La revisión de las corrugaciones de los rodillos a medida que cambian los requisitos de molienda es un aspecto que a menudo se pasa por alto en la molienda con molinos de rodillos.
Diferencial de velocidad de rollo
El diferencial de velocidad de los rodillos es la diferencia en la velocidad de rotación entre los dos rodillos de un par y es una de las principales razones por las que los molinos de rodillos producen una molienda con menor variación en el tamaño de las partículas en comparación con los molinos de martillos. El diferencial crea un efecto de cizallamiento entre los rodillos que corta el material en lugar de aplastarlo. El uso de un diferencial mayor reducirá la cantidad de finos producidos, mejorando la variación estándar. La relación diferencial está limitada por el tamaño de las poleas que se pueden ajustar dentro de la protección del molino de rodillos. Las poleas son poleas en los ejes de los rodillos que están conectadas por correas para hacer que los rodillos giren a velocidades designadas. Si las poleas son demasiado grandes, entrarán en contacto con la otra polea en el eje del rodillo emparejado o con el marco/protección de la máquina. La relación diferencial de velocidad más común al moler en molinos de rodillos es 1,5:1.
Paralelismo de rodillos y nivelación de rodillos.
Para maximizar la vida útil de los rodillos y lograr un rendimiento constante de un extremo a otro, cada par de rodillos debe estar paralelo y nivelado, es decir, alineados horizontalmente. Si los rodillos no están paralelos, triturarán el material fino en un extremo y grueso en el otro y también se desgastarán de manera desigual. Lo mismo ocurre con los rodillos que no están nivelados.
Normalmente, el ajuste de nivelación sólo se realizará cuando se cambien los rodillos operados o en alguna condición de desequilibrio significativo (como pérdida de cangilones elevadores y tornillos que aparecen en el espacio entre los rodillos).
Cuando los rodillos no están paralelos o nivelados, el material tiende a "deslizarse" en el espacio entre los rodillos hacia los extremos más abiertos. Este exceso de material puede comenzar a acumularse en el espacio entre los rodillos y provocar un desgaste acelerado. Intentar obtener un pulido fino cuando los rodillos no están paralelos o nivelados puede hacer que el extremo "cerrado" (o el centro de los rodillos si están fuera de nivel) entre en contacto metal con metal. Es posible comprobar de forma rutinaria el paralelismo de los rodillos utilizando un medidor de espesor cuando la máquina está abierta o comparando los tamaños de molienda de las muestras tomadas de cada extremo de los rodillos.
Equilibrio entre pares de rodillos
En máquinas con doble o triple par de rodillos, es necesario equilibrar el trabajo realizado entre los pares de rodillos para evitar el desgaste prematuro de uno de los pares de rodillos. Cuando se maneja adecuadamente, cada par de rodillos se desgastará aproximadamente al mismo ritmo. Al utilizar una corrugación "escalonada" en los rodillos rápido y lento (con corrugaciones más gruesas en el rodillo rápido), los cuatro (o seis) rodillos estarán listos para la corrugación al mismo tiempo. Cambiar todos los rollos a la vez suele ser la forma más eficaz de aprovechar el tiempo y el esfuerzo necesarios para realizar un cambio de rollo.
Figura 5: Para eliminar la acumulación en la abertura del rodillo superior, abra ligeramente los rodillos superiores y cierre los rodillos inferiores para obtener el tamaño de partícula final deseado. Imagen cortesía de CPM Américas »
Los rodillos deben operarse de tal manera que se evite la acumulación de material en la abertura cuando el molino esté funcionando a plena
capacidad. Por lo general, esto no es un problema cuando los rodillos están en buenas condiciones, ya que las corrugaciones tirarán fácilmente del material y la carga del motor limitará el rendimiento. A medida que las corrugaciones, especialmente en los rodillos superiores, se vuelven desafiladas, perderán su eficacia para tirar del material y el material puede comenzar a acumularse en la abertura del rodillo. Esta condición debe evitarse ya que el deslizamiento del material en la abertura del rodillo acelerará significativamente el desgaste del rodillo. Si la capacidad del molino disminuye o la carga del motor no aumenta cuando se aumenta la velocidad de alimentación, es muy probable que el material no pase por los rodillos superiores. Para maximizar la capacidad y extender la vida útil de los rodillos, abra ligeramente los rodillos superiores y/o reduzca la velocidad de alimentación para eliminar la acumulación en las aberturas de los rodillos superiores. Si el producto final es demasiado espeso, cierre los rodillos inferiores para obtener el tamaño de partícula final deseado (Figura 5).
Elementos básicos de mantenimiento del molino de rodillos.
Realice las siguientes comprobaciones con frecuencia para obtener un rendimiento óptimo del molino de rodillos:
• Comprobar el paralelismo de los rodillos.
• Verifique la tensión y alineación de la correa.
•Limpie los imanes del separador.
• Inspeccione visualmente los rodillos para detectar desgaste anormal, desigual o prematuro.
• Revise las placas laterales y los sellos de los rodillos para asegurarse de que todo el material pase a través de los rodillos.
Las placas protectoras laterales se colocan sobre los extremos de los rodillos para evitar que el material pase alrededor de los rodillos en los extremos, mientras que los sellos de rodillos son placas montadas en la parte superior de los rodillos para evitar que el material pase sobre los rodillos en la parte superior.